Ice research at the TUHH
The ice laboratory is a part of the strength laboratory of the institute for ship structural design and analysis of the Hamburg University of Technology. The institute is under the direction of Franz von Bock und Polach and regarding the topic ice we focus on ice-structure interaction, ice mechanics and wave-ice interaction. Most experiments are conducted in large scale, where powerful hydraulic pistons push ice against structures of full-scale size or close to it. The main objective is to investigate the occurring phenomena in the interactions and to be able to reproduce the experiments later numerically.
In the past years we have developed an ice production process that allows to repeat experiments with very similar results.
Furthermore, Franz von Bock und Polach is the chairman of the ITTC specialist committee on ice. ITTC stands for International Towing Tank Conference and works on international standards and guidelines for testing and assessing ships and marine structures through physical and numerical modelling.
The laboratory is used for both funded research projects as well as student research projects.
In addition to ice, we work in our laboratory with fatigue of structural elements (e.g. welds), corrosion, ultimate strength of marine structures and many more.
Facility Description of TUHH
The laboratory has a 20" reefer container which serves as production unit for large ice samples (1 m diameter) and storage. Here ice samples can be shaped and sawed as well as thin sections can be prepared.
The cold chamber has a hydraulic piston that reaches through the roof to ensure that the hydraulic oil is not cooled. The hydraulic cylinders on top can be exchanged depending on the load and piston velocity. Here we can facilitate piston velocities down to mm/min to generate ductile failure and deformation (left) and up to 1 m/s for brittle failure (right).
The hydraulics test stand can apply loads up to 4 MN and is suitable to simulate large-scale (almost full scale) ice-structure interactions. This test stand is not temperature controlled which requires swift and fast testing procedures to avoid warming and temperature impact on the ice.
The drop tower is also not cooled and is used for fast and high energy ice-structure impact scenarios. Such scenarios are found in propeller-ice interactions (HealthProp Link), ship ice-breaking or wave-ice-structure interaction scenarios.
The laboratory of the institute for ship structural design and analysis of the Hamburg University of Technology (TUHH) has several testing units for ice.
The lab is located in Hamburg (district Harburg) on the main campus of TUHH.
Production unit
The laboratory has a 20" reefer container which serves as production unit for large ice samples (1 m diameter) and storage. Here ice samples can be shaped and sawed as well as thin sections can be prepared.
Cold chamber with hydraulic test stand
The cold chamber has a hydraulic piston that reaches through the roof to ensure that the hydraulic oil is not cooled. The hydraulic cylinders on top can be exchanged depending on the load and piston velocity. Here we can facilitate piston velocities down to mm/min to generate ductile failure and deformation (left) and up to 1 m/s for brittle failure (right).
Large hydraulic test rig
The hydraulics test stand can apply loads up to 4 MN and is suitable to simulate large-scale (almost full scale) ice-structure interactions. This test stand is not temperature controlled which requires swift and fast testing procedures to avoid warming and temperature impact on the ice.
Drop tower
The drop tower is also not cooled and is used for fast and high energy ice-structure impact scenarios. Such scenarios are found in propeller-ice interactions (HealthProp Link), ship ice-breaking or wave-ice-structure interaction scenarios.
Selected projects
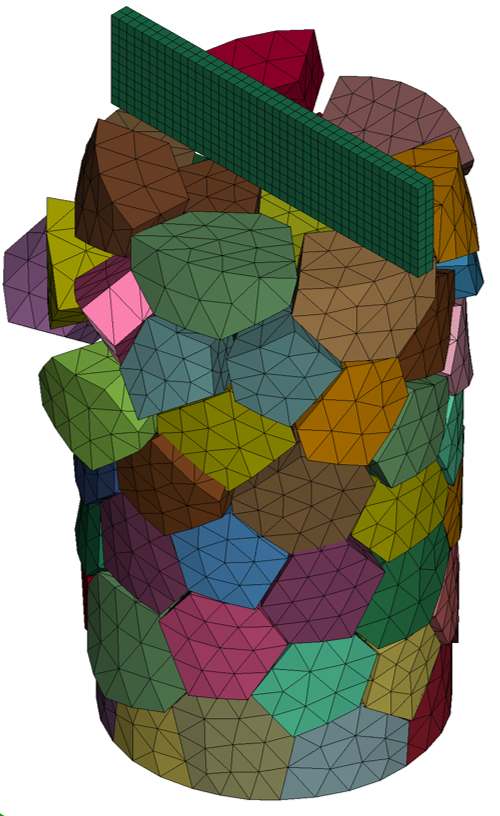
Propeller-ice interaction
In the project HealthProp (MARTera co-fund scheme, H2020) we seek to model the ice failure against a propeller blade. The project is based of a series of experiments with increasing complexity that are modeled in the process. The image shows the simulation of an experiment where a balde edge cuts a cylindrical ice specimen. The main goal of HealthProp is to develop a digital twin platform - by combining intelligent sensors, data acquisition systems and fault detection algorithms through physical and data-driven models in the cloud - towards monitoring the propulsion system and drive line of ships in Arctic and Antarctic operations, with the aim to improve the system reliability and increase the operational safety in harsh environmental conditions. The TUHH develops in Healthprop a new ice load model for propellers. The research is a combination of large scale experiments an simulations. With the results in our work packages we seek to predict the ice loading on a propeller more accurately and therewith the longterm impact regaring fatigue and wear of components. The project is part of MarTERA - an ERA-NET Cofund scheme of Horizon 2020 of the European Commission - and the Research Council of Norway (Project no. 311502), the Federal Ministry for Economic Affairs and Climate Action of Germany (Project no. 03SX519B), and Department of Science and Technology of South Africa, through the HealthProp project.– Jonas Behnen (former researcher), Angelo Böhm (researcher), Franz von Bock und Polach (PI)
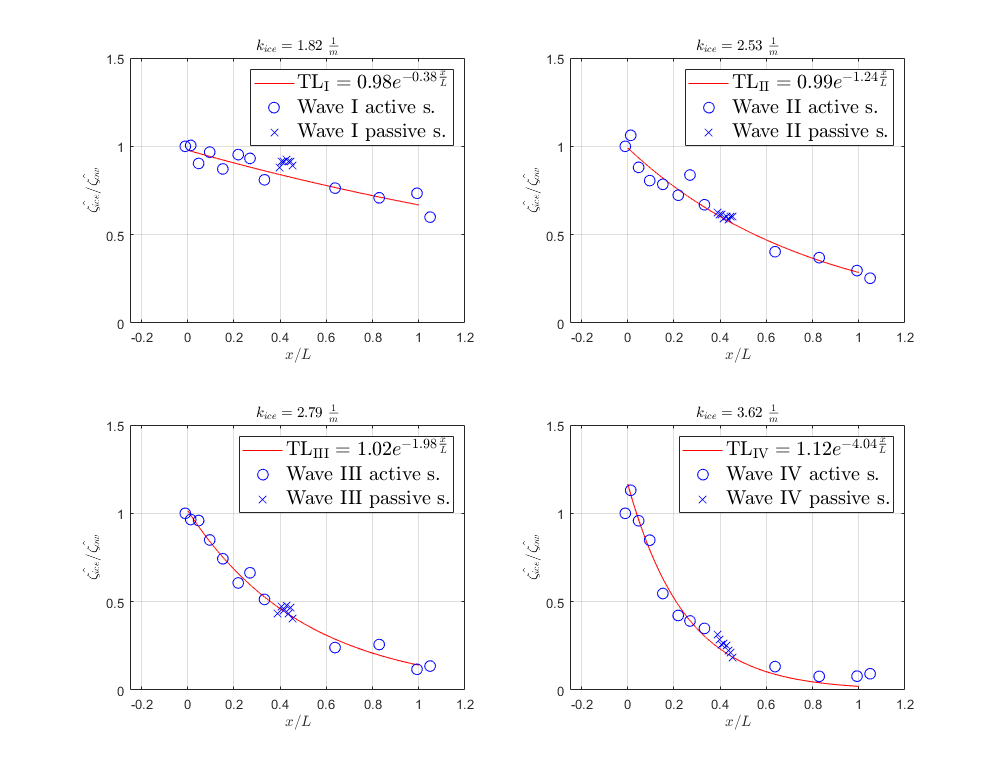
Non-linear wave-ice interaction
During a test campaign in the Ice Tank of the Hamburg Ship Model Basin (HSVA), we investigated the damping of regular waves in non broken model ice. Both active ultra sonic and passive video tracking sensors were used to detect the properties of the waves. By distributing narrow spaced passive sensors over a five meter distance on the solid ice sheet, it was able to reconstruct the wave number and to derive the dispersion relation in ice. In the left figure the exponential decay of the wave amplitude for the different wave numbers is shown. The decay represent the damping of the waves due to the ice sheet and corresponds well to other research. Furthermore, the trend of increasing exponential coefficient with increasing wave number is visible by comparing the four figures which indicate that higher wave frequencies are stronger damped by the solid ice sheet. Hartmann, M. C. N., von Bock und Polach, R. U. and Klein, M. ‘Damping of Regular Waves in Model Ice’, 2020, ASME 2020 39th International Conference on Ocean, Offshore and Arctic Engineering. Research project "Nonlinear wave-ice-interaction" funded by the Deutsche Forschungsgemeinschaft (DFG, German Research Foundation)– Moritz Hartmann, Franz von Bock und Polach, Marco Klein (PI)
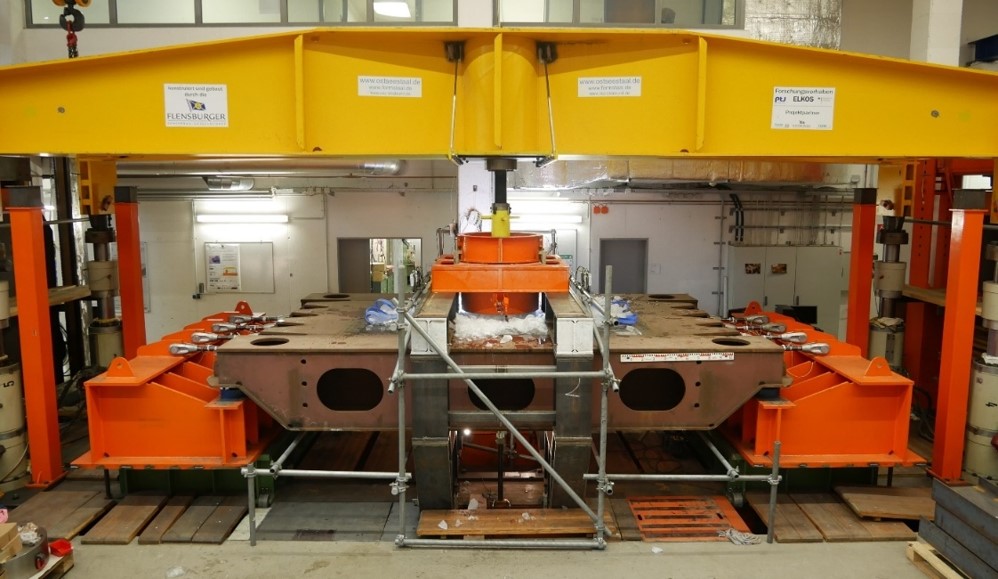
Large-scale Ice-Structure Interaction Tests
Ice loads pose a significant hazard to ship and offshore structures. Unlike in automotive industry, for example, full-scale collision tests of ships are hardly possible. In order to be able to investigat critical ice-induced deformations of real ship structures in a laboratory envirement the ice extrusion test was developed at the Instiute of Ship Structural Design and Analysis at Hamburg University of Technology. During the experiment, an ice specimen is pushed out of a confining pipe (orange) against the considered test structure. In previous campaigns, both quasi-rigid and ice-strengthed panels, such as those commonly used for ships in the Baltic Sea, were investigated. Plastic deformations of the panel up to 87 mm were achieved at 4 mm/sec cylinder velocity. The experimental data are now available to improve the understanding of ice-structure interaction and for the development of new or the enhancement of existing numerical models to enabable reliable simulatins of ice loads for e.g. risks accessment, operational guidance or rule development.– Hauke Herrnring
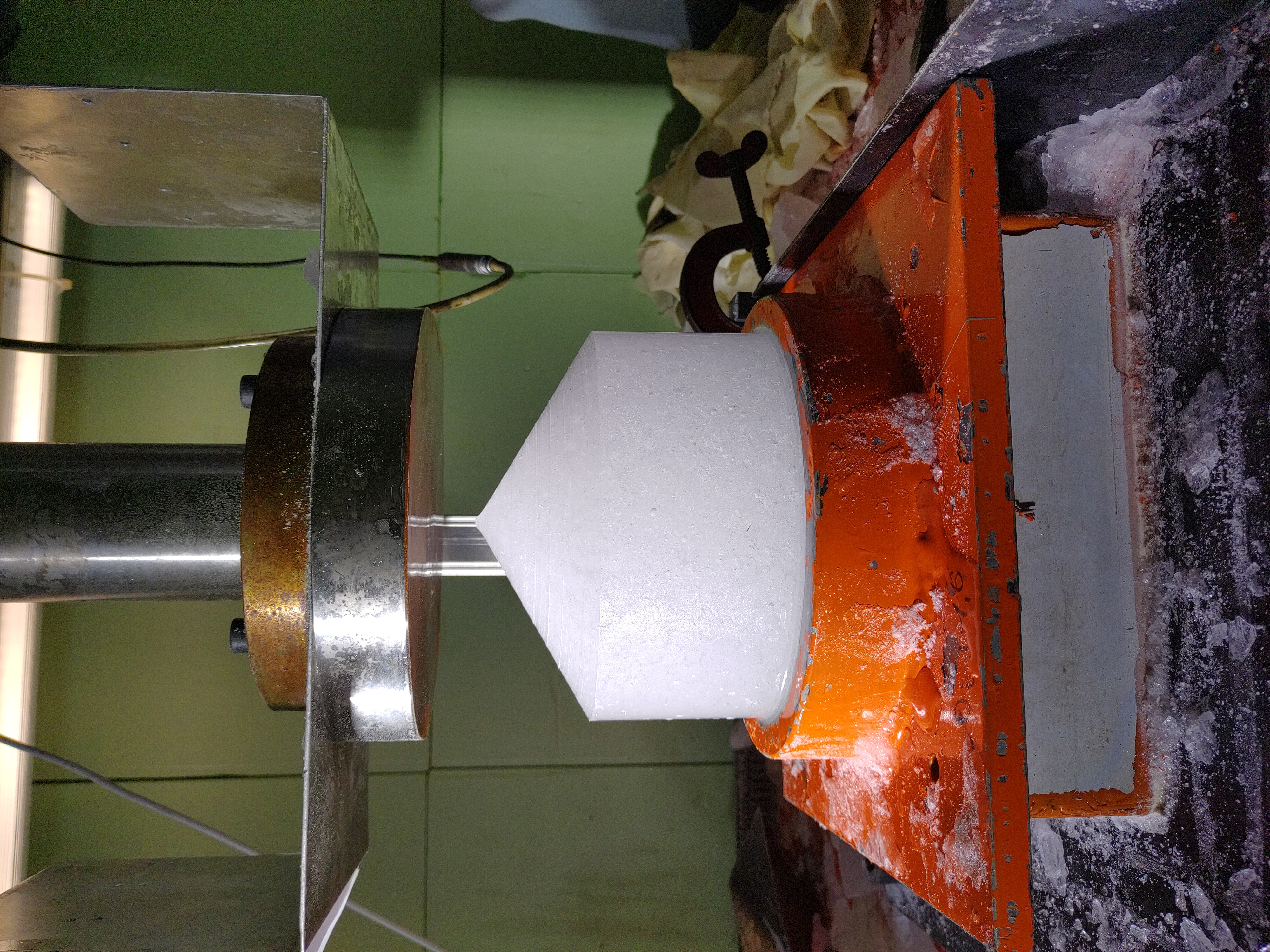
What role does the ice shape play in ship collisions scenarios with icebergs or ice floes?
In our project IceShape we investigate experimentally and numerically ice-structure interaction scenarios with different shaped ice specimen. This serves to find the potentially most dangerous impact case in ship-ice collision scenarios. To analyze the influence of different geometry parameters we conducted experiments in model scale with 17 different ice shapes. Therefore two different test rigs were utilized to be able to test a high range of interaction velocities of 10 to 2000 mm/s. In both test setups the ice was crushed by a steel plate, that was in one case hydraulically driven and in the other case released from a predefined drop height and fell vertically guided onto the specimen. The force acting in vertical direction was recorded by load cells and the displacement of the steel plate was measured by a displacement transducer. A comparision of the maximum measured forces showed a high dependency on the ice geometry. Ice geometries with a large parallel contact area to the steel plate (like a cylinder) showed the highest forces with values up to over 300 kN. Whereas ice specimen with no or small parallel contact areas (like a cone or dome) showed very low forces with values below 50 kN. The experiments showed further that even a inclination of 1° between the contact area of the ice and steel plate leads to a drop in max. load of over 50%. With respect to the interaction velocity is was found, that low velocities between 10 and 100 mm/s lead to similar results. Interaction velocity of 2000 mm/s lead, depending on the ice shape, to loads that are 70% higher compared to lower interaction velocities. In a next step the experimental data will serve as a database to validate the numerical simulation and further develope it to be able to apply it to full-scale ship-ice collision scenarios.– Franciska Müller